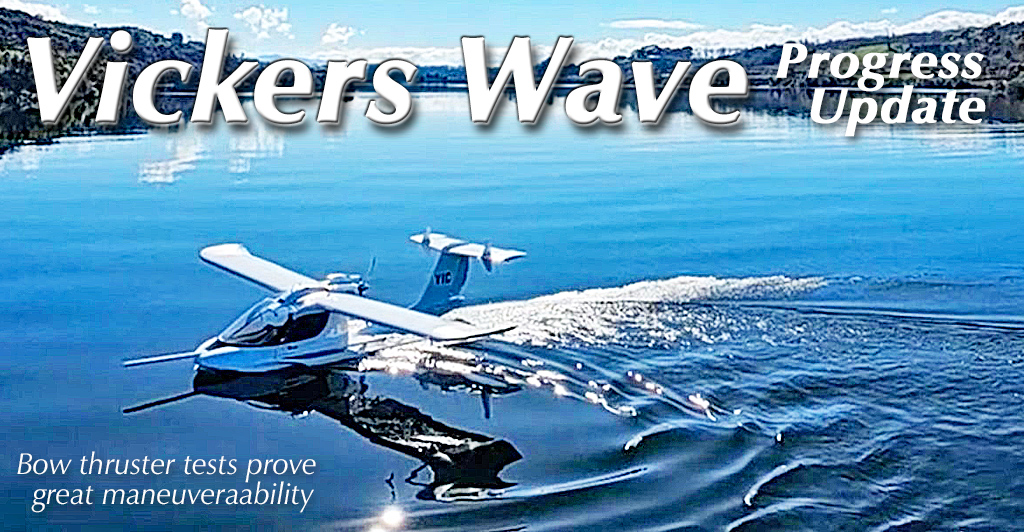
Winter is coming, so naturally, it’s time to start thinking about seaplanes… right? It always seems weird to write about water-based activities as frost begins to envelop the northern two-thirds of the country. Yet winter is when all the big boat shows happen because buying new vessels requires advance planning. It’s also pleasant to think about spring and summer while snow flurries fly. For many years I’ve written about this sector and names like Searey, Seamax, and Aventura (all in nearby image) have long been the leading brands. Now the first two are in financial trouble and the last has decamped to Brazil from Florida. Whatever is going on, Vickers Wave may represent a breath of fresh air. In articles last fall and this spring, I gave overviews of the entire LSA seaplane market (read here or here). Vickers Wave Update Vickers previously noted, “Wave has finished its flight testing, resulting in a 120-knot cruise and useful load of 750 pounds powered by a Rotax 916iS (reviewed here).” “A frequently asked question I receive is, ‘What is taking so long?’,” begins Paul Vickers.